In response to the overwhelming interest and enquiries received during our Fuel for thought webinar "Is this Methanol’s moment?" , we're thrilled to present an exclusive video interview by our host Craig Eason with Sobhith Hariharan, our global shipbuilding expert.
Our video interview takes a deeper dive into the most popular and thought-provoking questions that emerged during our "Fuel for Thought" Methanol webinar. We've carefully selected and addressed the questions that resonated most with the audience during the webinar. This engaging conversation is designed to provide clarity, insights, and valuable perspectives on the topics raised pertaining to methanol as an alternative fuel for shipping.
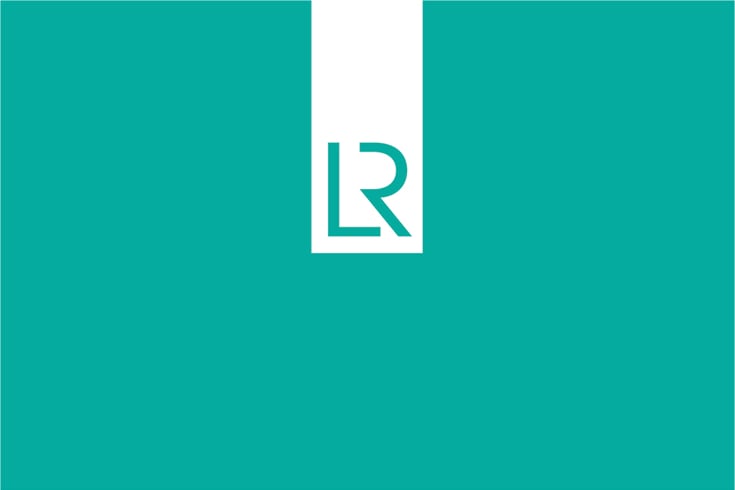
Methanol webinar Q&A
Methanol's lower energy density (14.9 MJ/L) compared to HFO (35 MJ/L) means vessels may require over 2.4 times the volume for equivalent endurance. This impacts vessel design and fuel operation, possibly requiring the owner/operator to adopt various means – either larger Methanol fuel tanks or choosing Methanol for specific voyage legs. This must be handled while ensuring compliance with and the applicable IMO regulations as well as emission trading schemes such as EU-ETS/FuelEU Maritime, posing operational challenges for ship owners. In contrast, LNG offers higher energy content but requires cryogenic storage, specialised tanks, insulation, and compromises cargo capacity compared to Methanol fuel.
The production of grey methanol involves reforming natural gas with steam, resulting in higher well-to-wake emissions compared to VLSFO. However, there's a transition plan from grey to blue and then to green methanol, requiring substantial investments. Grey methanol, despite higher emissions than VLSFO, still emits less than grey ammonia or hydrogen, but it surpasses other fossil-based fuels in terms of well-to-wake emissions.
Methanol's availability in over 100 ports and successful trials like the first methanol bunkering operation in Singapore and Rotterdam indicates its potential growth. As demand for methanol increases at various ports, especially in areas where methanol-fuelled container ships operate, this could pave the way for more vessel types to adopt methanol as a fuel. Additionally, we might see a change in bunkering patterns and methanol bunker availability in locations close to where newer green methanol production facilities are proposed, for example Port Said or other areas in the Middle East.
Addressing the hazards and challenges of methanol bunkering is a top priority. Adapting industry expertise from methanol loading and unloading as currently undertaken by tankers (Methanol carriers/product tankers) to provide bunkering for various ship types is crucial. This includes assessing safety parameters and potential ignition sources near bunkering locations among several others. During bunkering operations, risks such as methanol leakage and associated toxicity, fire risk due to its low flashpoint, and fuel contamination are managed through design and operational measures, aligning with the approach taken for LNG as a fuel. Safety and risk reduction remain paramount.
Methanol as a fuel shows lower NOx emissions, but it doesn't mean that engines directly comply with Tier 3 NOx abatement requirements. Aftertreatment is necessary when operating in NOx emission-controlled areas. Established technologies like SCR and EGR used in HFO or MDO-fuelled vessels can be applied, and new approaches like MAN's water injection aimed at reducing combustion chamber temperatures and associated NOx could be applied. However, no single solution fits all, and the choice depends on the engine and vessel size, with implications for fuel consumption when using an abatement system.
Methanol application in retrofit vessels, like the Stena Germanica, has proven successful. However, conversion poses technical challenges, especially related to endurance, fuel tank size, bunkering, safety systems, and engine conversion. Retrofitting is technically challenging and cost-intensive. Engine makers are becoming confident in converting electronically controlled engines to methanol or other alternative fuels. The process involves changes to fuel injection systems,adding auxiliary systems such as a sealing oil system, enhancing safety systems, upgrading control systems for combustion control, plus also addressing NOx emissions control. The overall cost depends on vessel type, the availability of conversion kits for the specific engine and extent of engineering design to be undertaken, making it challenging to estimate at this stage.
Addressing methanol corrosion is a significant challenge. The experience from chemical tankers and product carriers carrying methanol as cargo provides insights into necessary precautions, including suitable coatings for tank interiors. Similar considerations apply to piping, valves, and components, with specific requirements for materials to prevent corrosion. Compatibility analysis is ongoing, supported by in-service experiences from methanol-fuelled vessels. These insights inform rule development, offering assurance in mitigating corrosive challenges associated with using methanol as a fuel.
Back to: Methanol hub