Nikolaos Apodiakos represents the third generation of bulk carrier owner, Victoria Steamship Co. Ltd, which was set up by his grandfather in London in 1946. Today, as agents for ship management company Blue Planet Shipping, the company has a fleet of 13 bulk carriers ranging in size from 50,000 dwt to 95,000 dwt. Most of the ships have been built over the last ten years.
The company is unusual in a number of ways. As shipping undergoes a spell of unprecedented change today, it is invariably the largest owners and operators which can afford to assess the viability and test the merits of new technologies. But Blue Planet, with modest resources and a comparatively small fleet, has been pursuing such a strategy for close to eight decades. Its principals have prioritised the environmental impact of the company’s activities and have, in some instances, explored technologies long ago that are only now the focus of broader development.
It was Nikolaos’ father, Costas, for example, who embarked on a voyage of discovery in the early 2000s that started with investigations into wind power for merchant ships and subsequently a range of other technologies. Costas was supported in these pioneering endeavours by the company’s Technical Director, Spiros Contopoulos, who remains closely involved today.
The birth of Anemoi
It was in 2007 that Costas started wind power experiments, first in New Zealand and then at Warsash in Southampton. A series of investigations and trials were undertaken leading to full-scale Flettner rotor sail models being built and tested on land and at sea. This process resulted in the setting up of London-based Anemoi Marine Technologies. In Greek mythology, Anemoi is the name for the gods of the four winds.
In a groundbreaking 2018 project in China, four Anemoi sails were installed on the company’s Ultramax bulk carrier, Afros, the first-ever wind power installation on a bulker; a vessel classed by LR. The 17m-high sails are installed on a rail deployment system and controlled from the bridge. Meanwhile, the company’s bulk carrier, Axios, an 82,000 dwt Kamsarmax, also classed by LR, was built ‘wind ready’. The sails have a transverse rail deployment system.
Anemoi’s presence at Posidonia this year demonstrated that its technology is gaining ground, both for existing ships and newbuildings. Recent installations include an 82,000 dwt Kamsarmax bulker, TR Lady, owned by a Tufton Oceanic company and chartered to Cargill. The vessel has three 24m-high rotor sails mounted on Anemoi’s patented transverse rail deployment system; class approvals were also granted by LR.

Meanwhile, one of the world’s largest mining companies, Vale S.A., has installed five 35m-high Anemoi sails on the 400,000 dwt Sohar Max, the world’s largest ore carrier. Owned by Oman’s Asyad Shipping, the sails use Anemoi’s folding deployment system to reduce impact on air draft and cargo operations.
Vale’s bulk carriers typically trade between Brazil, the Middle East, and China – routes on which wind energy can yield significant benefits. The mining company is expecting fuel savings of about 6%, with the relevant impact on air emissions reduction.
In another Valemax project, four similarly-sized Anemoi sails have been installed on Berge Bulk’s 388,000 dwt Berge Neblina. The sails, with a similar folding arrangement, were installed quayside at You Lian Dockyards (Shekou) Ltd.
The company’s sail technology is also suitable for smaller vessels. Earlier this year, Anemoi won part of a UK Government grant from the Clean Maritime Demonstration Competition. The group comprises Victoria Steamship, Connected Places Catapult, and Frazer-Nash Consultancy and the money will be used to develop smaller sails for vessel types including Handysize bulk carriers, product and chemical tankers, and ro-ros.
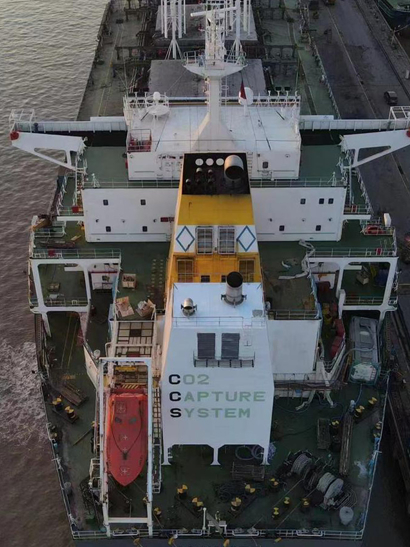
Other ship efficiency initiatives
Meanwhile, in a pilot carbon capture and storage (CCS) project, Victoria Steamship’s 95,300 dwt bulk carrier, Alkimos, built in 2013, was retrofitted with a Sinotech CCS installation earlier this year. According to Technology Director, Spiros Contopoulos, there are two principal capture technologies. One that absorbs CO2 using Amine liquid solution, whilst at the same time having a system onboard to separate the CO2 from the Amine collecting liquid CO2 in cryogenic independent tanks onboard. The other that collects the mixture of CO2/Amine which can then be separated ashore. Both processes relying heavily on shore facilities to remove the CO2 capture from the vessel and replenish the vessel with new Amine depending on the system.
In other energy-saving projects, the Victoria Steamship team have tried and tested a range of technologies and assessed their potential returns on investment. The company has tested propeller boss cap fins, a means of improving water flow around the propeller and reducing torque losses. Efficiency gains of around 2-3% have been demonstrated. Swirl propeller ducts have also been installed with very good results producing savings between 4-5%.
Other technologies tried and tested include variable frequency drives to optimise pump operation and engine room fan ventilators, producing a fuel saving averaging between 0.5-0.6 mt of fuel at sea and in port, an equivalent saving of about 2.5% overall saving at sea, on an Ultramax vessel. Shaft generators to use main engine power to generate electricity, rather than auxiliary engines, which produce a saving of about 0.7mt of fuel per day on a Kamsarmax, equivalent to a 3% overall saving at sea, plus maintenance costs savings on generator engines. Advanced hull coatings, and propeller silicon coating for better and lasting performance. Wind Generators that could produce up to 200kW at sea and in port depending on the wind strength. Adding all these technologies onboard, which have low ROI, one can achieve at least a 10-12% saving in fuel.
Taken in isolation, none of these technologies is likely to have a major impact on ship operation. But as the Greek company’s team point out, shipping is contending with a raft of new regulations relating to energy use and emissions, with more on the way. Shipowners and operators cannot afford to continue on a ‘business as usual’ basis – the pursuit of energy efficiency is of paramount importance.
Reflecting on the wide range of energy-saving technologies identified and tested by the managers of the Greek shipping group, Nikolaos Apodiakos stresses the importance of collaboration between partners over the years, including support from LR. “For the industry to overcome the challenges of today and tomorrow, it is imperative that such collaboration and partnerships grow and develop further,” he said.
New rules for Emissions Abatement Carbon Capture and Storage
LR has introduced rule requirements for the design, construction, and installation survey of EACSS (Emissions Abatement Carbon Capture and Storage) which address the safety risks they may present to the vessel, covering aspects such as materials, structure, containment, piping, refrigeration plant, electrical, control, safety systems, vessel integration and manufacturing.
To support innovation, where the use of other carbon capture technologies or deviation from the requirements is proposed, compliance with the goals and functional requirements needs to be demonstrated. LR's risk assessment (or Risk Based Certification) process will help demonstrate that ‘risk’ from a proposed design can be ‘accepted’ by LR and the regulator (i.e. National Administration, flag), ensuring that the overall level of safety provided is maintained (to mitigate any adverse effect to the persons onboard, the environment or the ship).
Any appropriate solution can be provided which requires justification to demonstrate safe design and operation. Where there is no experience/or limited experience and knowledge, a pure alternative design approach/risk based approach will require a comprehensive design process.
To explore the practical options for your fleet, learn more about our Ship Retrofit Solutions and how they can help you make the right choice. Additionally, our Retrofit Research Programme offers cutting-edge insights into how retrofitting can significantly enhance your vessel's efficiency and sustainability.