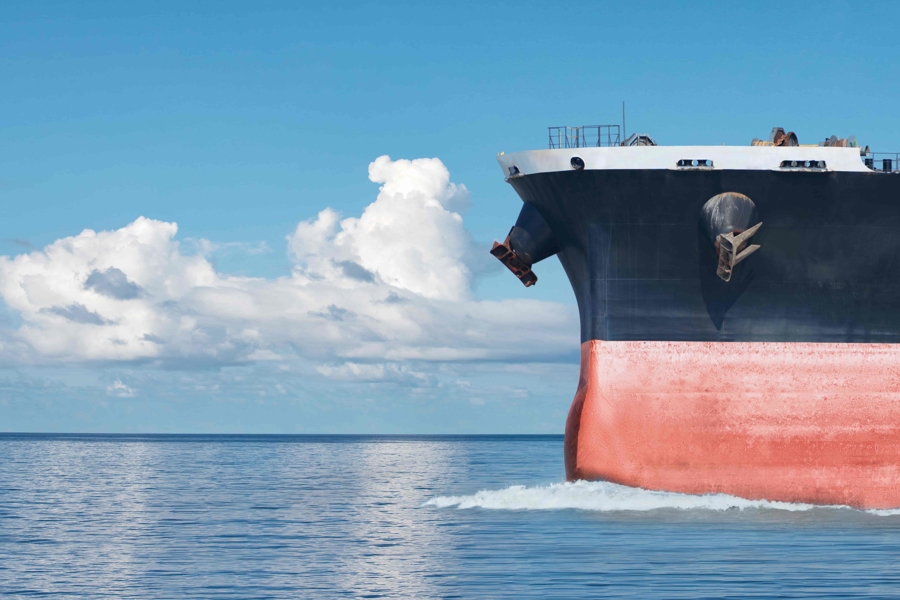
Improve the efficiency of your fleet and lower undersea noise pollution by reducing excessive vibrations. LR offers expert support to manage noise and vibrations for both new builds and existing marine and offshore assets using in-field measurements, numerical predictions, and extensive troubleshooting experience.
- Noise and vibration measurements: Worldwide accredited measurement of ship and propeller noise and vibration using portable hydrophones, microphones, accelerometers and data loggers to give you actionable recommendations.
- Noise and Vibration predictions: Finite element (FE) analysis and noise assessments to calculate vibration response, for actionable advice and options on passenger and crew comfort onboard the vessel.
- Passenger and Crew Accommodation Comfort (PCAC) Measurements and Review: Noise and vibration measurements conducted at specified operating conditions to evaluate compliance with PCAC notation.
- Airborne noise (ABN) measurements and predictions: Outdoor noise measurements in free sailing and harbour conditions to evaluate ABN compliance.
- Underwater management plan development: Recommendations based on an evaluation of components likely to generate noise and vibration.
- Vessel underwater radiated noise prediction: Underwater noise predictions for Class compliance for hull, propeller and other potential noise sources, based on vibro-acoustic finite element analysis, computational fluid dynamics, statistical energy analysis and ray tracing.
- Environmental impact at specific locations: Accurate marine noise representations accounting for site-specific details such as bathymetry, multi-layer seabed properties, salinity and temperature profiles through wavenumber, parabolic equations, beam tracing, and normal mode models.
-
Mitigating underwater radiated noise (URN) from shipping: Expert advice on mitigating noise.
- Propeller cavitation testing, modelling, and analysis: Minimise cavitation and noise while maintaining operational speed at delivered power by predicting propeller URN under cavitating conditions and adjusting propeller blade loads through eddy flow simulation (DES) and Ffowcs Williams-Hawkings acoustic analogy (FWH) of the propeller plane