Floating offshore wind continues to gain momentum as more countries invite development further from their shores. The technology providers are responding with an array of new concepts suited to the harsher environments. However, there is a pressing need for new design requirements and certification schemes, as many of the novel components, sub-assemblies and interfaces cannot be assessed using conventional processes.
To help floating offshore wind consortia and their backers make the right choices, international working groups and offshore wind standard committees are devising appropriate guidance. LR is also working on its own recommended practice to support the development of floating offshore wind facilities, ensuring compliance with the regulatory requirements emerging worldwide. The Recommended Practice (RP) encompasses all the associated engineering disciplines and each phase of a project, from design through construction and operation, and will help the industry address the technology step-outs in this rapidly-advancing field, with 15-MW turbines currently under development.
In addition, LR offers two alternative methods for assessing the risks and uncertainties associated with floating offshore wind innovations. Both have attracted the interest of companies in the offshore/onshore oil and gas supply chain looking to diversify into renewable energy. The Certification through Technology Qualification (CTQ) program, dating back to 1995, applies to any novel technology or operational method that cannot be certified via conventional schemes. The three-stage process, which takes around 24 months to complete, involves verification, validation and a comprehensive performance review to help ensure a safe and reliable deployment in the intended environment.
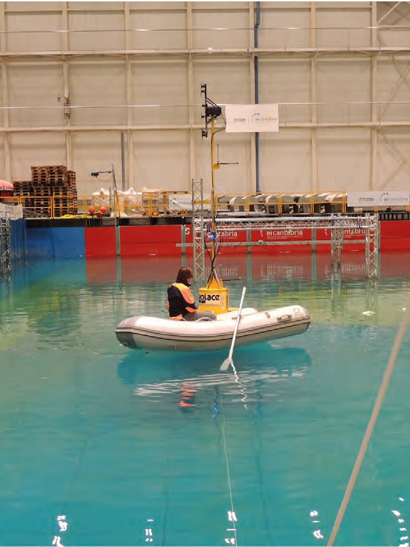
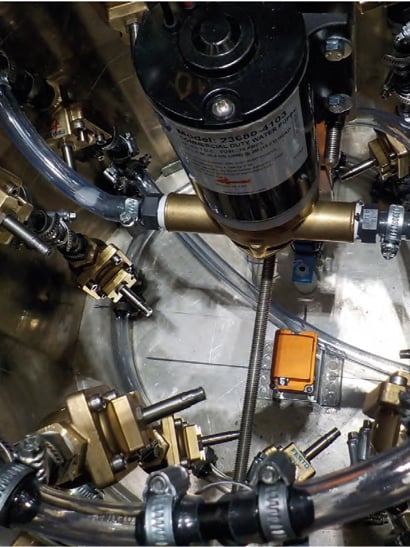
According to LR’s Offshore Technology Manager Mark Tipping, there has been a more noticeable increase in applications of late from the offshore sector for LR’s Approval in Principle (AiP) process. This covers the use of established technologies and principles in a different way to operate in an offshore wind setting. “So instead of qualifying a new technology, we are approving/qualifying the new concept and methodology being implemented. AiP involves verifying and validating a design against its ability to comply with relevant or recognised codes, standards or normative rules. It is typically used by the recipient to prove to various stakeholders that the concept is credible, from operators to finance providers, insurers, and regulators.”
“LR provides these services independently and indiscriminately to any company that might request them, whether the technology developer, the wind farm developer, a joint venture, or any other,” added George Kallenos, Clean Energy Commercial Manager. “AiP can be sought for a complete system or an individual system component. With a floating offshore wind turbine, for example, AiP could be applied specifically to the mooring lines.”
One technology that recently attained LR AiP following a two-year review is Seaplace’s CROWN active ballast control system. This has been designed to work with two types of CROWN floating wind turbine platforms developed by the company, one a reduced-draft spar, the other a buoy, and also with competing floating wind concepts. The system is used to ballast/de-ballast the unit, switching it from its transport draft to operational draft; and to partly or fully compensate the mean tilt created by wind loads, improving the unit’s stability. In addition, the control system can stabilise the platform following damage to a compartment, or keep it operational in the event of a valve or pump malfunction. The software allows for remote manual, automatic, or semi-automatic control.
Seaplace, based in Madrid, Spain since 1980, has 15 years’ experience developing solutions and studies for different types of platforms for offshore wind and renewable energy. The company, which employs more than 450 naval architects and engineers, also has a long track record providing engineering services to the offshore oil and gas sector for FPSOs, construction vessels, drilling rigs and mooring systems.
“Our reason for seeking AiP,” said COO and Naval Architect Jaime Moreu, “came from when we were showing the CROWN technology to developers and stakeholders: we realised how important it was for them to see third party validation. While some floating offshore wind developers have been working in the sector for years, others are relative newcomers that are less familiar with the technology. So it is key to have a third party confirm that what you are doing adds value to the industry. LR has a long and valued track record in the industry, and is a perfect match for this validation.” Tipping added: “The industry knows that LR is comfortable working with novel technologies that do not have a precedent. We can provide evidence, so people can relate to what is out there.”
“With the ant-heeling ballast control system (AHBCS), being able to validate the software to interested parties was another key factor in our choosing to apply for the AiP process,” Moreu explained. “We started the process with LR in summer 2019, splitting the AiP works into three main packages. LR helped with the majority: they analysed the ballast system both for the technology itself and how it operates with the CROWN buoy solution, which we think offers the best potential. With LR’s guidance, we prepared a set of documents which they could subsequently sign off and release for AiP.” The 11 documents started with a description of the safety philosophy and design principles of the AHBCS and its most relevant features, according to applicable rules and standards, with special attention paid to safety provisions and redundancy in essential equipment.
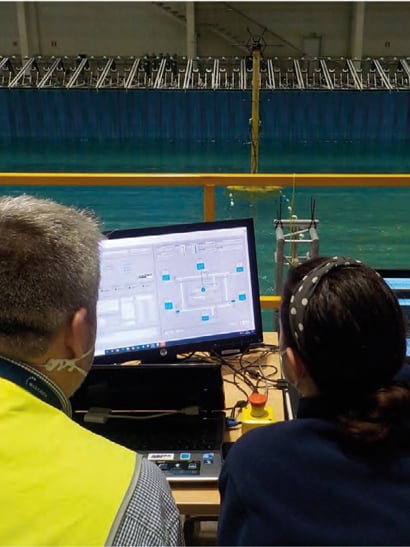
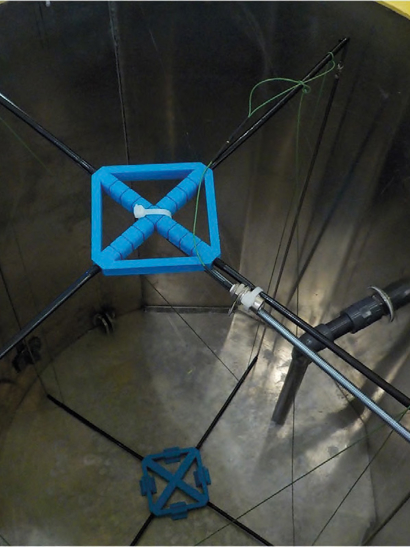
“Ballast control systems are in common use in offshore wind, they represent the most relevant active system from the platform side,” Moreu said. “We have conceived our system to be like level 2 in Dynamic Positioning, where there are three redundancy levels, from 1 to 3. While a DP1 system cannot operate in case of a single component failure, this is permissible with DP2, as you must still be able to maintain positioning in case of failure, and that is windour approach: the AHBCS performs even if a pump or valve fails. LR worked with Seaplace extensively to help ensure that any potential failure had no impact on the unit’s performance. And our ballast control system adds value, because it corrects the mean tilt produced by the wind, and simplifies the transport and installation marine operations. Furthermore, it allows the platform to be positioned over the port seabed for the turbine assembly, and can correct the heeling angle should flooding occur.” It’s also worth noting, Tipping added, “that demonstrating the unit’s operational stability proves a better bottom line to interested investors.”
“The tests we performed at IHC are fully representative of the anticipated operational lifetimes of the CROWN units,” Moreu continued. “The tests simulated years of operation, with just a few days needed for validation. Tests on both the CROWN buoy and reduced-draft spar ran for two months and employed the ballast system in many cases, with LR representatives in attendance on specific days when the focus was on proving the system’s correct performance. The floaters were 1/31 and 1/36 scale models crafted to withstand significant wave heights of up to 15 m and wave periods of 17 seconds, as might be expected in parts of the Atlantic Ocean. But we have also created a portfolio of floaters to perform well in different conditions, including the Baltic, Mediterranean and North Sea.” The ballast system is configured to work with other floating offshore wind turbine designs too, adjusting the number of pumps/valves in the system or adding more or less volumes of water, as required. “And having certification of the product with AiP can actually help other clients reduce the risk of their own concepts,” Moreu suggested.
Seaplace’s next step is to assemble a full-size demonstrator unit and to select a potential offshore test site by the end of 2021. LR aims to continue the relationship, supporting the company in CROWN’s next construction and operations phases and once in commercial service, potentially for all stages of the units’ lives.