As world energy patterns undergo unprecedented disruption, and key regions face possible shortages in the months ahead, many energy importers have turned to seaborne LNG as a replacement for interrupted supplies. The world has large reserves and, for Europe, friendly nations including the US, Australia and Qatar, with supplies available by sea to replace other imports, previously available by pipeline.
The dash for gas has prompted record contracting of deep-sea LNG carriers, with more than 240 now on order at the world’s seven specialist LNG builders. These yards – in South Korea and China – are booked up until 2027 and there is no scope for extra construction capacity in the short term. Other shipbuilders lack the expertise and are, in any case, already working at close to capacity.
Three generations of technology
Before I set out the specific challenge, I’ll briefly outline the structure of the current fleet. In approximate terms, today’s 650-ship deep-sea LNG-carrying fleet is made up of about 240 ships powered by steam turbines, around 190 dual-fuel diesel-electric (DFDE) vessels, and about 215 low- and high-pressure two-stroke units.
The first generation of steamers consists of elderly ships which are heavy consumers of fuel and do not have boil-off management systems. Therefore, their day rates are substantially lower than LNG carriers with other, more efficient propulsion arrangements. However, they do have one key advantage: they do not suffer from methane slip. So far, this is not a key concern for charterers.
The second generation – four-stroke DFDE engines – came next. Although they were substantially more fuel-efficient than steamers, they also have some significant shortcomings. They were available in high- and low-pressure configurations but suffer significant methane slip. In some conditions, some of these engines suffer from up to 15 times the level of slip compared with later engine designs.
Then, around the middle of the last decade, work began on developing a third generation of LNG propulsion, based on two-stroke engines. These are more efficient and generate significantly less methane slip. The first ships using this technology were commissioned in 2016.
The LNG carriers currently on order, and which will be delivered between now and 2027, are mostly being built in line with this third-generation engine technology. Some will also incorporate energy-saving features such as air lubrication systems, shaft generators (power take-off), and waste heat recovery.
Provided they have a high-quality containment system, these ships will be as efficient as is possible today. However, by the time some of them deliver around the middle of this decade, the technology they use will already be nearly ten years old.
The impact of price
In the early days of LNG transport, ships were built for specific projects and deployed on very long-term contracts, sometimes more than 20 years. LNG carriers were tied exclusively to supply contracts, built to the highest specifications, and financed as key components in those long-term contracts.
However, as the short-term and spot market in LNG has developed over the last decade, a new breed of independent LNG owner has arrived. The market is now far less focused on long-term supply contracts. Short-term and even spot charters feature in the market. Unlike the previous project finance arrangements, these new owners have funded assets themselves with financiers, rather than on the strength of future income streams.
The whole business of LNG transport by sea has undergone a transformation.
Since 2018, shipyards have enjoyed a strong market with strong prices. They have capitalised on steady contracting in various sectors and filled their berths with profitable deals. They had no wish to expand into a complex and challenging sector such as LNG because the upfront commitments were too great. Therefore, we are left today with just a handful of specialist builders which, as I say, are full.
When the first latest-spec LNG carriers were ordered and commissioned four or five years ago, they came at a price of about $180m. This stayed fairly level for some time. However, higher shipbuilding prices, more newbuild contracts, and now the rising prices of materials, have pushed the cost of a $180m ship up to about $250m.
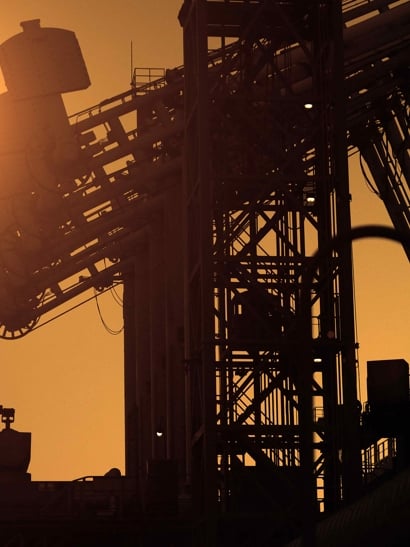
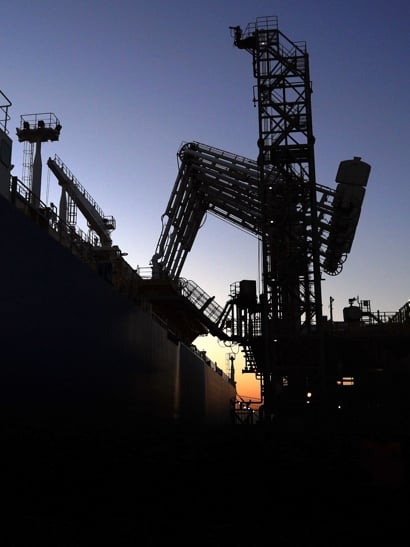
The hand of the accountants
The result is that most LNG carriers ordered recently are being built to specs as basic as possible, with few extras. Shipyards have the upper hand because building capacity is under pressure. They aim to build the simplest possible vessel and, if an owner – a potential customer – becomes insistent on non-standard features, he or she is likely to be shown the shipbuilder’s door. After all, there are plenty of other owners looking for slots and new ship prices are climbing by the day.
There are other forces at work, too. The LNG owners’ in-house money men look at the extra cost of optional extras such as waste heat recovery or power take-off and, in all probability, shake their heads. Why do we need it when nobody else is having it, they ask, especially when any extras come at a high cost?
In my view, this thinking is flawed. The most basic LNG carrier designs are likely to be the least attractive from a charterers’ viewpoint later in the decade because, in carbon efficiency terms, they will have the lower CII grades. If there are to be ‘stranded assets’, these will be among the first.
Let me give you an example. LNG carriers’ containment systems are one of the most important factors in ship efficiency. Last year, Lloyd’s Register approved a new advanced series of membrane containment – the GTT No96 Super +.
Although this is more efficient than other existing containment technologies and have been available for some time, it is only in recent weeks that builders/owners have started to offer/ask for them. Until recently, only one Japanese owner had specified the new containment system.
Why, when it was so much more efficient? The simple answer is price.
The CII framework
When the IMO’s carbon efficiency indicator (CII) regulation enters force in January, most existing LNG carriers will fall into categories C, D and E. Between now and 2026, they will need to achieve efficiency gains of around 11% just to maintain their grade. In 2026 the regulation will be reconsidered, and the improvements will be further strengthened.
However, when existing ships are initially assessed and new ones are commissioned, methane slip will not feature in the CII assessment. In the second half of the decade, however, it will be included. This will radically change the landscape because ships that fall into categories D and E risk becoming unemployable.
So, although the sector is absolutely essential to future energy transport requirements, the danger is that we have a bunch of stranded assets prevented from shipping LNG because of regulations designed to improve carbon efficiency.
What can we do?
I believe there are three options, two of which, to my mind, are out of the question: one, we build more efficient ships with the right technologies that help to meet CII requirements and replace large parts of the fleet. Clearly, this is impossible; the industry lacks both the construction capacity and the time to build them.
Two, we agree to rationalise our approach to climate targets and withdraw from aspirations on carbon efficiency. This is not possible either, environmentally or politically. Three, the industry ramps up efforts to develop new technologies that can be integrated and implemented on existing ships to bridge any carbon compliance gaps. These technologies will have to include high-grade boil-off management systems, methane abatement, shipboard carbon capture, wind and solar assistance, and energy saving retrofits.
Adapt or crash
I would like to give you a recent example of the type of initiative that, in my opinion, the industry needs urgently. Last year, Lloyd’s Register awarded Approval in Principle to Spanish LNG shipowner, Empresa Naviera Elcano, for its patented steam-to-hybrid conversion arrangement for ships with steam turbines. By integrating a four-stroke engine in parallel with the steam turbine, ships can be transformed from straight steamers to a hybrid propulsion arrangement, without the need to remove any parts of the original turbine equipment.
On top of the conversion, further substantial gains can be achieved by retrofitting a re-liquefaction plant, driven by a dual-fuel generator, to manage boil-off effectively. This would further enable savings and an improved CII profile.
We estimate that these projects would cost about 10% of newbuild prices prevailing today – in other words, about $25 million. But we calculate typical efficiency improvements of between 20-30%, resulting in a far more favourable CII assessment and a substantial life extension.
These converted steamers could benefit from up to another ten years of profitable employment. It would push back the end of ships’ lives from a date generated by their emissions profile to a date based on their structural lifecycle. They would not become stranded assets, allowing for a smoother fleet renewal schedule.
This is just one example of a strategy we urgently need. The alternative is a fleet that will face widespread carbon compliance issues from next year onwards, eventually forcing ships out of service during the second half of the decade. If we do nothing, we must brace for another more serious energy crash in which we have lots of LNG but no ships to transport it.