Shipping’s ambitions to reduce emissions have triggered efforts to operate using as little fuel as possible. In the same way that options for optimised sailings, weather routeing and energy saving technologies (ETSs) are being considered, so too has the humble hull come into focus. Accounting for around 70% of the structural design of a vessel, a ship’s hull has a considerable impact on vessel performance and a smooth, clean hull with an effective coating applied can help maximise operational efficiency.
Never before has vessel performance been more important than today, as new regional legislation in the form of the EU ETS (Emissions Trading Scheme) and international regulations such as the IMO Carbon Intensity Indicator (CII) rating system come into play, affecting charter party agreements and placing renewed emphasis on efficient operations.
Ensuring the surface of a hull remains as smooth as possible enables a vessel to cut through water with minimal resistance. The less resistance, the less fuel is required to power the vessel, resulting in reduced emissions.
But there are other factors incentivising a proactive approach to hull management.
Revised IMO guidelines relating to biofouling on a ship’s hull – the accumulation of aquatic organisms, such as molluscs and barnacles on ships’ hulls – adopted in July 2023, further expose the benefits of sailing with a well-managed hull in order to minimise the transfer of invasive aquatic species.
Heather Hughes, Lloyd’s Register’s Non-Metallics and Coatings Team Leader, and one of the experts that works with IMO, says that in recent years, she has seen a “step-change” to industry’s approach in hull efficiency and environmental protection. “There's been such a seismic shift in their thinking, and innovation in terms of what typically would be viewed as hull management has changed quite rapidly,” she tells Horizons.
“Hull management is vital to keep biofouling to a minimum and can be achieved through hull cleaning procedures and/or coating selection,” she says. “Not only can biofouling, such as molluscs and other aquatic life that affix to ship, create friction and reduce vessel performance, it can wreak havoc in delicate ecosystems and industry is taking this onboard,” she asserts.
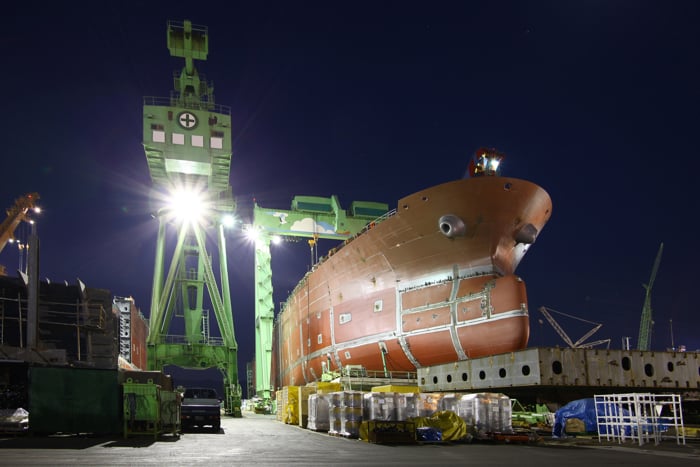
Industry standards
Hughes is part of a team of scientists and engineers at LR, that works with ship operators, owners and other shipping stakeholders to offer guidance on available technologies, provides assurance that technologies are delivering the desired outcomes and, importantly, creates new class notations (or standards) that companies can aspire to achieve.
As an example, LR has developed a Clean Hull notation introduced at the beginning of this year, to assess and verify that ship operators’ biofouling management plans are fulfilling the required criteria laid out by the IMO and enable operators to take proactive actions to reduce hull-induced greenhouse gas (GHG) emissions.
Sahan Abeysekara, LR’s Technical Specialist, Environment, was involved in creating this notation, and explains that it “brings together two otherwise isolated regulatory regimes – first, the reduction of GHG emissions and second, the prevention of the spread of invasive aquatic species. It also provides a platform to synergise the two during ship operations. With LR’s Clean Hull notation, ship operators’ efforts to reduce emissions and biofouling are recognised, they benefit from increased vessel performance, reduced fuel consumption and EU ETS tariffs, and at the same time are complying with biosecurity requirements”.
LR is also a member of the IMO-GEF- UNDP GloFouling Partnership, a global initiative that aims to implement the new IMO guidelines and improve biofouling management.
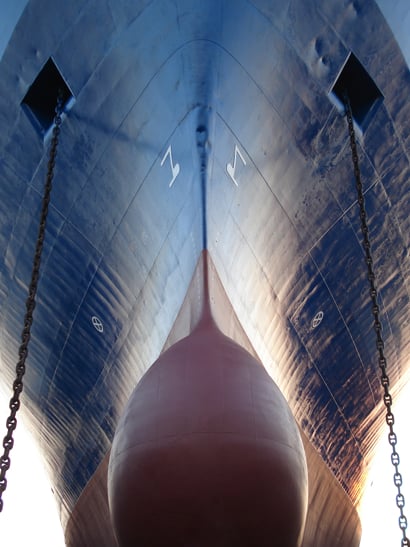
New type approval
Whilst the revised IMO guidelines are not mandatory, several regions already have restrictions in place regarding hull biofouling, with Australia, New Zealand and the US west coast amongst those to issue more stringent requirements.
With this in mind, Hughes is introducing a new Enhanced Antifouling Type Approval, which will gather the correct data to ascertain whether the coating still performs according to the coatings’ manufacturers claims pre and post cleaning.
The new type approval is currently being trialled on an LR client’s vessel and the data provided will “give assurance that the coating will perform and that it's compatible with the agreed cleaning schedules required for the vessel,” says Hughes, adding that these new IMO guidelines are centred on proactive hull cleaning at the slime layer stage and before shell fouling occurs.
And there is much to consider. A vessel’s hull is usually given a thorough overhaul during its five-yearly dry dock, when its cleaned and re-painted.
In the intervening years, in-water hull cleaning is required as build up of matter is rapid, with IMO stating that studies have shown that the biofouling process begins within the first few hours of a hull's immersion in water. However, this process creates its own challenges as the molluscs, barnacles and other aquatic life affixed to the hull are scraped off and released into the water.
Hughes observes that in-water hull cleaning to remove biofouling could increase as owners and operators take advantage of a clean hull to maintain their CII rating and charter party obligations. “ Capture and appropriate disposal of the organic matter scraped off the hull is essential to avoid its release into the water and consideration of these processes features in the revised recommendations from IMO,” she explains.
Performance benefits
Meanwhile, the commercial aspects of good hull management should not be overlooked.
Whilst LR is technology agnostic, Hughes acknowledges that an appropriate coating, taking into account a vessel’s idle periods and trading patterns (water temperature, for example, can significantly impact hull fouling levels), properly applied can offer notable emissions reductions.
Dogan Uzun, LR’s Ship Performance consultant, works closely with clients to assess their vessels’ performance through short-term sea trials and long-term monitoring projects to establish vessel performance and make comparisons before and after coating technologies or other ESTs are applied. By analysing the performance of the vessel before and after, the client can assess the efficacy of their investment in relation to business case for installation, environmental regulatory compliance and exposure reduction ( for example, EU ETS) and other contractual requirements.
“Every aspect of a vessel is coming under increasing scrutiny to maximise performance as far as possible,” says Uzun. “These days it’s not only about fuel savings, although that continues to be a factor. It’s about maintaining the commercial viability of a vessel and it’s a trend that is set to increase, especially as we move closer to 2030 and aim to meet IMO’s emissions reduction ambitions.”
Coatings for future fuels
There are many parts of a ship that require specific coating technology to ensure safe operations and protect cargoes, including anti-corrosive coatings to protect exteriors from rusting, ballast water tank coatings and also specific requirements for fuel tanks. LR is currently considering the many ways that coatings can assist shipping’s decarbonisation journey beyond those applied to ships’ hulls.
As we look to alternative fuels as a key pathway to net-zero GHG emissions, consideration must be given to fuel storage tanks onboard ship and also the storage units in which they are transported, explained Hughes. “The carbon steel tanks typically used in the carriage of traditional bunkers may not be suitable as we move towards other fuel types,” she explains.
“Two potential future fuels, methanol and ammonia, as well as liquid carbon dioxide (LCO2) (which can be captured and stored onboard in tanks) can have a deleterious effect on standard carbon steel tanks,” said Hughes. “So LR is looking at the possibility of using coatings to mitigate this.”