Additive manufacturing (AM), often referred to as 3D printing, could transform the landscape of shipbuilding and maritime operations with the potential to redefine production processes, reduce environmental impact, and enhance supply chain resilience. LR has been at the forefront of certifying this technology for a number of years, combining its extensive technical and regulatory expertise with the industry’s need for innovative solutions.
Unlike traditional manufacturing methods, which typically involve subtractive processes – where the material is removed and shaped into parts – AM builds components from the ground up layer by layer, based on digital design blueprints. This technology allows for tailored designs and minimises waste by using only the material required for each part. While AM has been well established in sectors like aerospace and automotive, it is relatively new in maritime, where traditional practices and regulatory challenges have slowed its adoption.
Lifecycle emissions
Decarbonisation in maritime is not just about alternative fuels or energy-saving technologies; it also extends to the materials and processes used throughout a vessel’s lifecycle – these are factored into a company’s Scope 3 emissions (a reporting requirement for European companies from next year).
This is where the potential of AM becomes transformative. By enabling the production of lighter components through processes like topology optimisation – where the material layout is optimised to maximise performance – AM could potentially reduce a vessel’s overall weight, leading to improved fuel efficiency.
Another environmental benefit of AM is the potential for on-demand, localised production. By digitally sending blueprints and producing parts closer to their point of use, shipping costs and related emissions are reduced. "Printing a part at a port facility, rather than shipping it from a centralised factory, has clear sustainability benefits," Saxty notes. This localisation is especially relevant in regions with limited access to traditional manufacturing supply chains, such as remote ports or offshore installations.
AM technology can also manage obsolescence by reverse-engineering outdated parts, reducing the need for high-inventory storage and improving the overall supply chain resilience."
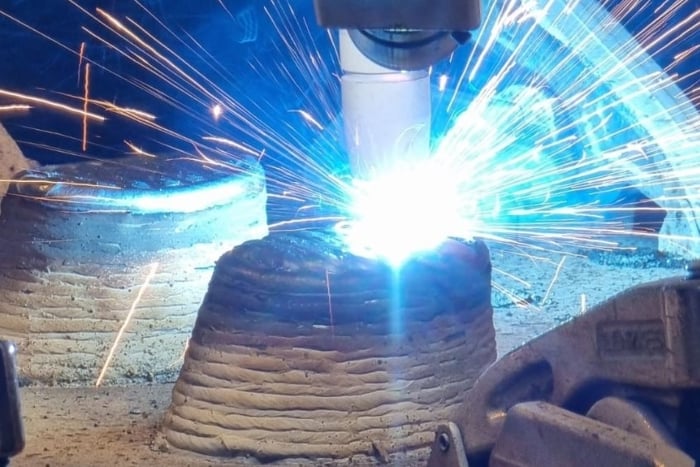
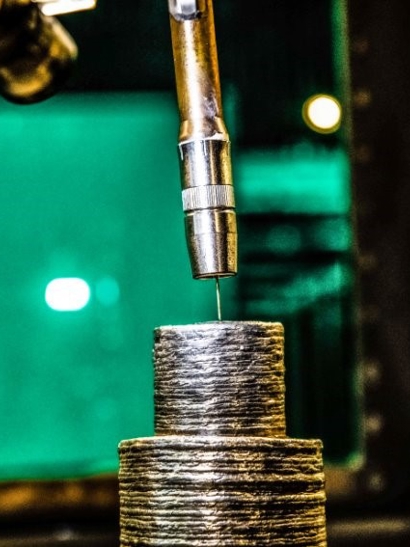
Certifying an evolving technology
LR is uniquely positioned to enable the maritime sector’s adoption of AM, predominantly by certifying AM-produced parts to ensure they meet industry standards. However, as Saxty points out, LR’s approach also emphasises flexibility: “We’re using guidance notes rather than strict rules, which allows us to support clients more dynamically as the technology evolves.”
LR’s guidance documents cover multiple aspects of AM, from material specifications to performance testing. These notes provide a framework for clients, enabling them to navigate AM’s regulatory and technical complexities. LR collaborates closely with both established manufacturers and AM specialists, acting as a bridge between traditional maritime production and innovative, AM-based techniques.
Beyond certification, LR has been active in the educational space, helping to raise awareness about AM's potential. It has supported PhD research and partnered with institutions on projects that explore AM applications in marine environments, highlighting LR’s commitment to making AM a mainstream, trusted manufacturing alternative within the maritime industry.
MariLight project
The MariLight project, an Innovate UK-funded joint industry initiative, represents a practical exploration of AM’s potential to contribute to maritime decarbonisation. This project is exploring the potential to create lighter, more fuel-efficient ships by using AM processes to produce optimised components. “The principle behind MariLight is straightforward,” Saxty says. “If we make vessels lighter, we make them more fuel-efficient.”
One of MariLight’s primary goals is to develop components that not only reduce vessel weight but also reduce the associated through-life emissions without any performance reductions.These components are designed using topology optimisation, creating forms that retain essential structural integrity while minimising mass. This process results in parts that look more organic in appearance, resembling muscles or tendons rather than traditional, block-like structures.
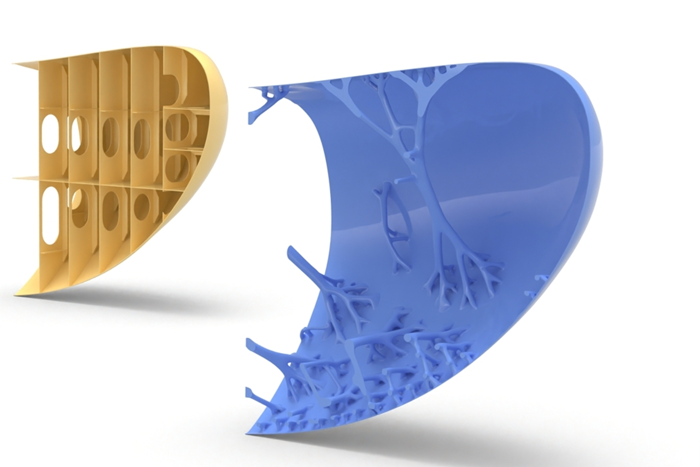
MariLight’s initial phase, completed in September 2023, involved a feasibility study that validated AM’s capacity to produce components at the required scale for marine applications. The project’s second phase, currently in progress, seeks to further develop the technology, with the goal of producing full-scale components for pre-deployment trials by March 2025. Although these components won’t yet be installed on active ships, they will undergo rigorous testing to ensure they meet industry standards.
Saxty elaborates on LR’s role in the project: “We’re involved as both a regulatory partner and a technical advisor. It’s essential that these components comply with marine standards, even if they’re produced through an unconventional method. Our role includes overseeing testing and verification to ensure that the AM parts deliver equivalent, if not superior, performance to traditionally manufactured ones.”
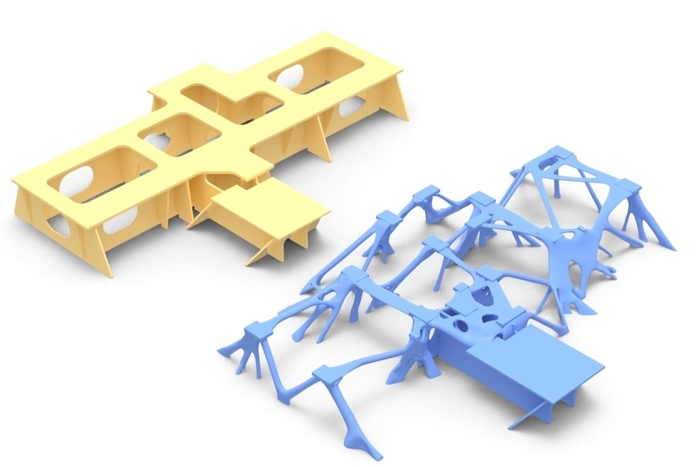
Barriers to adoption
Adopting AM on a larger scale in maritime is not without its challenges. The industry needs to address a number of hurdles, including upscaling AM processes to meet the size and durability requirements of maritime components and aligning production with marine safety standards. Additionally, LR and other stakeholders are working to standardise AM certification processes, especially for large-scale components like propellers or other structural ship features.
As Saxty explains, AM’s benefits go beyond environmental impact, supporting the digitalisation of manufacturing, reducing lead times, and potentially cutting costs in the long term. “In the next five to ten years, I see AM establishing itself as an alternative manufacturing approach in certain maritime segments, especially in regions or sectors where traditional supply chains are less established,” he predicts.
While mainstream adoption may take time, especially in regions with well-established shipbuilding practices, projects like MariLight highlight the potential for AM to drive both innovation and sustainability in maritime.