Amid the current surge in interest in converting ships to use methanol – with more than 100 ship conversions ordered last year – it is easy to forget that the first methanol conversion occurred nearly a decade ago.
A methanol frontrunner
In 2015, the Stena Line ro-pax cruise ferry Stena Germanica had methanol fuel tanks installed and began the conversion of its four Wärtsilä Z40 four-stroke engines to use the fuel, making it the world’s first methanol-fuelled passenger ship.
Based on that experience, Stena Line chose to work with LR on two further retrofits. Stena Superfast VII and Stena Superfast VIII will each have two out of four engines converted for methanol, with bunkering, storage, fuel supply, and supporting systems also adapted for the new fuel. LR has already issued Approval in Principle for the retrofit design based on its ShipRight Risk-Based Certification Stage 2. To leverage LR’s expertise in methanol fuel across the ship lifecycle, both roros will be transferred to LR class.
The rationale for the initial conversion nearly ten years ago was very different to today’s, driven by incoming regulations limiting sulphur (SOx) and nitrous oxide (NOx) emissions. Current ship conversions are driven by decarbonisation demand, with operators aiming to use renewable methanol to reduce exposure under the European Union’s Emissions Trading System, comply with emissions intensity requirements under the forthcoming FuelEU Maritime regulation, or to contribute to the IMO long-term ambition of reaching net-zero emissions from international shipping by or around 2050.
Whatever the reasons behind their conversion decisions, today’s shipowners and ship operators can draw important lessons from the pioneering project that brought the world’s first methanol retrofit into service – and the long-term collaboration that has seen Stena Germanica using the fuel successfully and safely for the past nine years. We worked closely with Stena Line across the design, construction, and commissioning of the methanol-fuelled ship, as well as providing in-service technical support. We now offer the most profound experience of methanol retrofitting in any class society.
Experience is important, and it seems as thought Lloyd’s Register has the experience when it comes to retrofits. When we speak to some suppliers and partners who have not been involved in these projects, it feels like we are having those initial discussions about the Germanica all over again.
Preparing for success
Today, planning a ship designed to use methanol fuel is covered by IMO’s International Code of Safety for Ships using Gases or other Low-flashpoint Fuels (IGF Code). Methanol-fuelled ship designs and equipment are required to have an equivalent safety to ships and technology using conventional fuel, and the interim guidelines contained within the IGF Code explain how this is to be achieved and assessed. But in 2015, there was no IGF Code or any other regulatory guidance on building methanol-fuelled vessels.
The first challenge then, was to establish a process for certifying the safe design of the converted vessel. The project team used a set of provisional rules for classifying methanol-fuelled vessels, which required a risk assessment to be undertaken to a recognised standard (for example, ISO 31010: Risk management - Risk assessment techniques) and in accordance with Lloyd’s Register’s ShipRight procedure Assessment of Risk Based Designs and associated annexes.
We coordinated large stakeholder meetings with members, including ports, national maritime authorities and technology suppliers - notably Wärtsilä, which was responsible for converting the vessel’s engines, as well as shipyard Remontowa and piping specialist Uwira. At these meetings, hazards were identified, and mitigation measures were agreed upon. Today, the risk-based approach still applies as methanol fuel – and conversions in particular – remains relatively new. However, the introduction of prescriptive rules under IMO’s IGF Code and LR's rules for methanol-fuelled ships has clarified many of the risks.
LR’s ShipRight Risk Based Certification (RBC), outlined in the diagram below, has been refined over the intervening years. The process, which takes shipowners from initial design through to construction and in-service assessment, fulfils the requirements of is consistent with requirements described in IMO Guidelines on alternative designs and arrangements, and means that owners of retrofitted vessels can be assured that their conversion will end with a safe and compliant ship.
Safeguarding innovative designs
Today, the technologies, materials, ship structures and equipment arrangements needed to enable the safe use of methanol fuel are relatively well-known after years of experience with methanol-fuelled ships, including Stena Germanica. But when Germanica’s conversion was first conceived, there was little knowledge in the maritime sector of how methanol could be used safely.
As an example, the types of rubber compatible with methanol were not widely known. This meant that the project team needed to conduct its own investigations into the suitability of materials for seals. That process was replicated across all the technologies and materials used in the conversion design, with the investigation sub-divided between suppliers to accelerate the process.
Ensuring the safety of the system was another prime consideration for such a novel project. A notable example is the tanking arrangements on Germanica. Because the shipowner wanted to maintain the resale value of the ship, the conventional fuel tanks were kept in place, meaning new space had to be found for the methanol tanks. The toxicity and flammability of methanol meant that new tanks would also need to be positioned to minimise the risk of a leak.
As a result, the new methanol tanks were eventually built inside ballast water tanks and protected by a water-filled cofferdam. Today, class rules provide for a less challenging design proposition. Cofferdams are required around the tanks, except on those surfaces bound by shell plating below the lowest possible waterline and other fuel tanks containing methyl/ethyl alcohol, as well as the fuel preparation space. Alternative proposals can also be considered if they provide an equivalent level of safety and meet the intent and functional requirements of the rules (see LR's Low Flashpoint Fuel Rules, Appendix LR1, Part A, Section 2.3).
We supported and approved each design element of the Germanica conversion, including the novel material selections and technology arrangements. Across the design process, all partners significantly built on the knowledge needed to make methanol fuel use a more viable option for shipping today.
Supporting the conversion
Stena Germanica’s conversion was divided into two stages. In the first stage, the entire methanol fuel line from the tanks to just before the engine were installed during drydocking. In the second stage, the engines were converted one by one, first in 2015 and subsequently as overhaul periods passed. At each engine conversion, LR was onboard to ensure installation conformed with the approved plans.
After certifying the final design of the ship, we certified that all components produced before the drydocking had been built in compliance with the design. When the ship was in drydock, the construction of components at the yard and the installation of equipment was further certified. Once the conversion was completed, the ship secured flag and class approvals following a sea trial.
The table below details a suggested timeline for an alternative fuel conversion project, including a description of the work conducted across the stages and the certifications and approvals involved. For more in-depth detail on retrofit projects and technologies, download our Engine Retrofit Report.
Lessons from real life
In-service learnings onboard Stena Germanica quickly delivered insights into the safe use of methanol as fuel. For example, the original leak detection arrangements had to be reconfigured for level detection rather than pressure sensors because it was identified that methanol remains a liquid for a longer-than-expected period before evaporating to a gas.
One early service challenge was to ensure that the piping needed as part of the methanol fuel system was robust enough to endure real-life voyage conditions. As the fuel preparation room was separated from the engine room as a safety provision, a long pipeline was needed. The steel piping was also heavier than for conventional fuel lines as it was double-walled to contain potential methanol leaks. Structural support for these new lines had to be adjusted to withstand the vibrations that were encountered once the vessel was in regular service.
As with the engine conversions, changes to structural supports needed to be carried out while the vessel was in service, without the logistical support available for drydock projects and while fitting around the ferry’s busy service schedule. In these instances, our field surveyors were able to draw on the experience of their colleagues who had assisted in the design approval and site supervision during the conversion. Their deep understanding of the vessel arrangement and methanol system played a valuable role in addressing the teething issues. The experience and expertise gained throughout the organisation is one element that still sets LR apart. Today it is still the only class society to have classed a vessel retrofitted for methanol.
As would be expected on such an innovative project, other important elements have been updated through experience. Fuel valve and safety valve designs have been refined to use materials that are more suited to the high pressures of methanol fuel piping and injection, for example.
Bunkering expertise has also advanced throughout the years. Stena Germanica bunkers methanol regularly in Gothenburg, allowing it to fulfil IMO’s global and regional NOx and SOx emission requirements. In 2023, it was part of the first ship-to-ship transfer of methanol in Gothenburg, the first such transfer to a ropax ship. With an eye to future greenhouse gas emissions compliance, the ships have also participated in a trial during which it bunkered blue ammonia, derived from fossil ammonia, with carbon from the production process captured.
The final crucial part of the puzzle is the maintenance regime. With new procedures ranging from wearing protective equipment to taking particular care while inspecting pipe surfaces, there has been a steep learning curve for crew.
These lessons will be harnessed by Stena Line as it extends its use of methanol to other vessels in its fleet. And for LR, which has continued to provide classification services and technical support to Stena Germanica, the experience it has gained can now support other shipowners and ship operators as they transition to using methanol as a fuel.
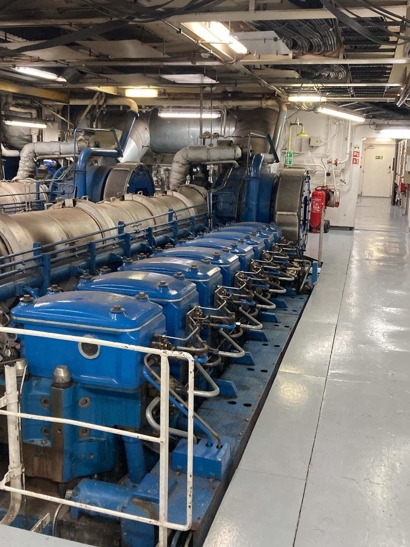
Applying a decade of experience
Over the past eight years, all parties in the original project have built on their early learnings. We have developed full class rules to support future conversions, hired specialist personnel, and are creating comprehensive guidelines for the substantial number of alternative fuel retrofits expected in the coming years.
As methanol conversions become part of the palette of solutions for maritime decarbonisation, LR’s decade of experience in supporting Stena Germanica means that it is ready to support shipowners preparing to start their own methanol-fuelled journeys.